金刚石磨片电镀单价(查看)_金刚石磨盘电镀
2023-02-07 09:03:09
金刚石薄膜的优点金刚石薄膜的优点是可应用于各种几何形状复杂的刀具,如带有切屑的刀片、端铣刀、铰刀及钻头;可以用来切削许多非金属材料,切削时切削力小、变形小、工作平稳、磨损慢、工件不易变形,适用于工件材
金刚石薄膜的优点
金刚石薄膜的优点是可应用于各种几何形状复杂的刀具,如带有切屑的刀片、端铣刀、铰刀及钻头;可以用来切削许多非金属材料金刚石磨片电镀,切削时切削力小、变形小、工作平稳、磨损慢、工件不易变形金刚石工具电镀,适用于工件材质好、公差小的精加工。主要缺点是金刚石薄膜与基体的粘接力较差,金刚石薄膜刀具不具有重磨性。
带柄磨头/小砂轮:磨头的种类很多,有陶瓷磨头,有橡胶磨头,供应商可以根据磨料和结合剂的不同进行选择;磨头有很多形状,而且每个公司对磨头形状代号没有统一,本文只列举了目前比较常见的形状供选择。“数量”属性是专门为磨头套装分类设置的,收集了目前比较常见的套装数量供选择金刚石锯片电镀。
金刚石表面金属化的实现方式
金刚石表面金属化的实现方式、表面金属与钎料的匹配和选择、钎剂和气体介质的选择等关键技术还需进一步成熟和优化。金刚石工具的使用效率与寿命除取决于金刚石磨粒被镶嵌的牢固程度外,还与胎体的耐磨性有关。
胎体本身强度的高低、金刚石在胎体中的分布状态、金刚石的浓度等都会对胎体的耐磨性产生影响,所以,如何使胎体达到理想的状态也是今后工作中值得注意的问题。
影响金刚石成核生长的两方面
磨料磨具中从影响金刚石成核生长的热力学和动力学方面考虑,主要有:衬底(基片)材料、衬底(基片)的预处理、衬底(基片)的炉内处理、沉积气源(气体中碳的浓度)、衬底(基片)温度、气体压强以及氢原子在沉积中的作用。
在这些因素中,对成膜的质量金刚石磨盘电镀,沉积速率都有影响,但是由于沉膜过程的复杂,各种不同的制备方法与工艺参数又互相关联,彼此之间又有差异,各工艺参数对学和金刚石膜的质量和沉积速率的影响都还没有特定的规律和精辟的解释。
CFRP加工用金刚石镀附工具
适宜地将基体和增强材料结合起来从而形成可控性机械特征是复合材料的一个特色。碳纤维增强塑料由于其优越的抗拉强度、比湿度、抗腐蚀性而广泛应用在工业机械如汽车、直升机、器械和铁路车辆等领域。此外,CFRP材料在航天领域是一种基础的结构材料,可以减轻飞机机身重量从而提高燃料效率,节省维护成本。
在航天领域,和CFRP材料有关的加工都会应用金刚石镀附工具。金刚石镀附钻,用于CFRP材料的精密钻孔。由于轴向力沿着纤维板叠层方面施力,钻孔时CFRP材料容易出现分层。
随着切削工具磨损的加剧和碎屑粘附在切削刃上,钻削时的抗钻强度也逐渐增大,CFRP材料过度受热,强度也由此降低。为解决这一问题,就不可避免地要应用到金刚石镀附钻。
金刚石磨头基本结构与应用范围介绍:
金刚石磨头是以金刚石磨料为原料,分别用金属粉、树脂粉、陶瓷和电镀金属作结合剂,制成的中央有通孔的圆形固结磨具称作金刚石磨头(合金磨头)。下面,我们就一起来了解一下金刚石磨头基本结构与应用范围。
金刚石磨头基本结构:
金刚石磨头结构一般由工作层、基体、过渡层三部分组成。工作层又称金刚石层,由磨料、结合剂和填料组成,是磨头的工作 部分。过渡层又称非金刚石层,由结合剂、金属粉和填料组成,是将金刚石层牢固地连接在基体上的部分。
基体,用于承接磨料层,并在使用时用法兰盘牢固地夹持在磨床主轴上。一般金属结合剂制品选用钢材、合金钢粉作基体;树脂结合剂选用铝合金、电木作基体。由铝、钢或电木加工而成,起支承工作层和装卡磨具的作用。磨头成型质量的好坏和使用精度的高低都与基体有很大关系。
金刚石磨头应用范围:
由于金刚石磨料所具有的特性(硬度高、抗压强度高、耐磨性好),使金刚石磨具在磨削加工中成为磨削硬脆材料及硬质合金的理想工具,不但、精度高,而且粗糙度好、磨具消耗少、使用寿命长,同时还可改善劳动条件。因此广泛用于普通磨具难于加工的低铁含量的金属及非金属硬脆材料,如硬质合金、高铝瓷、光学玻璃、玛瑙宝石、半导体材料、石材等。
金刚石磨头除了应用于低铁含量的金属及非金属硬脆材料加工,还应用于玻璃、陶瓷、铁氧体、半导体材料等硬脆性材料和金属材料的研磨加工、硬质合金材料的外形加工、电解磨削加工,以及磨削加工中心用金刚石钻头的磨削等重负荷切割,大大提高了生产效率。
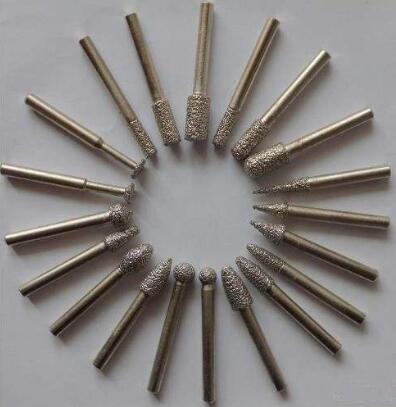
金刚石磨头粒度及其选择
粒度是指金刚石磨料的颗粒尺寸。对用筛选法获得的磨粒来说, 粒度号是用一英时长度上有多少个孔的筛网来命名的。例如, 12«粒度是指一英时长度上有十二个孔,余类推。而用Wxx 表示的微粉则是磨粒的实际尺寸。按照新修订的金刚石磨料粒度标 准,每种粒度号对应的磨粒尺寸如表2。
表2 粒度号及对应的磨粒公称尺寸(JB 1182—71)
金刚石磨料粒度的选择主要与加工表面光洁度和磨削生产率有关。 '当工件的磨削余量大,要求切削而工件表面质量要 求不髙时,例如去毛刺等,可选择14»〜24»的粗粒度金刚石磨头。
当磨头和工件接触面积较大时,要选用粒度組一些的砂 轮。例如,磨削相同的平面,用磨头的端面磨削比用磨头的周 边磨削选的粒度要粗些。
磨削有色金属和软金属比磨削钢件时所用的粒度要粗一些。一般的外圆和平面磨削选用36#〜70#粒度。外圆磨削大批生产时,例如磨曲轴轴颈,选用36»〜46»粒度。薄壁零件磨削时容易发热,此时,粒度要选得粗一些。
粒度较细的金刚石磨头一般用于磨削余量小、光洁度要求高的零 件。例如,刀具的刃磨一般采用60«〜100«粒度。螺纹磨削等则 用细于80»的粒度。
一般来说,随着粒度变细,磨削后的工件表面光洁度提 髙,但粒度对光洁度的这种影响只能就一定范围来说。我国上海机床厂和其他许多单位的工人和技术人员,经 过反复的试验和实践,通过对机床进行调整、改装、改进修整 方法,用较粗的46»〜80»粒度的陶瓷磨头同样磨出了 V12以上 的高光洁度,而用W10〜W20的细粒度树脂或橡胶结合剂加石 墨填料的磨头可以磨出V14的高光洁度。
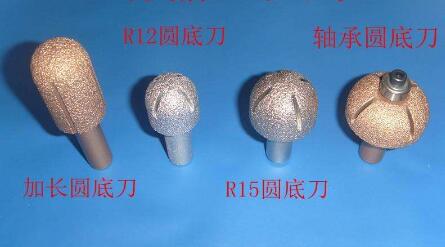